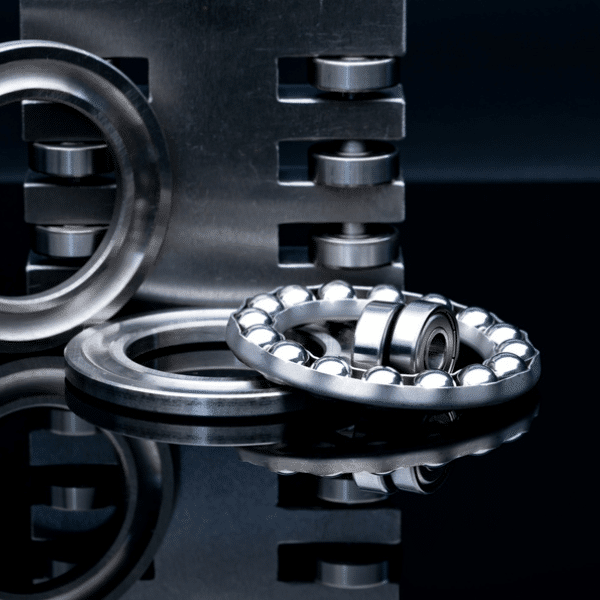
Learn bearing load types, calculations, and determination techniques to improve performance, avoid failures, and prolong mechanical system life.
Learn bearing load types, calculations, and determination techniques to improve performance, avoid failures, and prolong mechanical system life.
Understanding bearing loads is key to mechanical systems that depend on precise load determination for performance and bearing life. Bearings efficiently handle predicted forces without causing undue stress, deformation, or wear when axial, radial, combined, and centrifugal loads are accurately calculated. This is especially important in high-speed, high-impact, or misalignment-prone applications.
Angular contact and thrust bearings can handle axial loads. On the other hand, deep groove ball bearings and roller bearings can better deal with radial loads and lateral forces. Moreover, dynamic and static load ratings let engineers choose bearings that match system needs without exceeding material restrictions or temperature thresholds, which affect fatigue life.
Radial load is the force perpendicular to the axis of a shaft or bearing. It places stress on the bearing’s outer diameter. Excessive radial bearing loads from gears, pulleys, or wheels lead to non-uniform load distribution which can internally preload the bearing and significantly reduce internal clearance.
Radial loads play a vital role in high-speed machinery. Poor design directly results in rapid wear or catastrophic failure. For instance, electric motors endure steady radial loads from rotor weight and belt or pulley forces, which can prematurely fatigue the bearings if not properly managed. Cylindrical roller bearings and deep groove ball bearings are well-suited for handling radial loads, with basic load ratings exceeding hundreds of kilograms. In large conveyor systems, roller bearings offer superior performance due to their larger contact areas between rolling elements and raceways.
Axial or thrust load acts parallel to the shaft’s axis. It is toward or away from the source and impacts bearings differently. The load is common in gearboxes, elevators, and hydraulic presses, pushing or pulling along the shaft’s axis, and without suitable bearings, unwanted movement occurs. For example, thrust bearings in hydraulic cylinders endure the force from the piston. They need high axial load capacity to avoid damage or misalignment over repeated cycles.
For another example, axial loads must be controlled in automotive wheel hubs. Braking and cornering apply thrust forces that demand high durability. An angular contact bearing with a contact angle of 25° or more helps manage axial loads due to its load distribution across rolling elements. If axial loads are not handled, the result can be misalignment and accelerated bearing wear.
> What Type of Bearing is Best Used to Sustain Radial and Thrust Loads?
> Understanding Axial and Radial Loads: Key Differences and Bearing Selection
Combined bearing loads occur when radial and axial forces act on a bearing. Such load type is prevalent in wind turbines, automotive suspensions, and machine tool spindles. That’s where the component’s weight and thrust forces influence performance. For example, wheel bearings in a car suspension must support the vehicle’s weight (radial load) while absorbing lateral forces during cornering (axial load).
Tapered roller bearings and angular contact bearings are specifically designed to accommodate combined loads, distributing forces effectively in both directions. In wind turbines, main shaft bearings manage radial loads from rotor weight and axial loads from wind drag on blades.
Load Calculation Basics
Accurate determination of bearing loads is essential for optimizing mechanical system reliability. Load calculations evaluate static and dynamic forces, including their direction and magnitude. Engineers apply principles of statics and dynamics and use finite element analysis (FEA) to simulate loads in complex systems. For example, FEA effectively calculates transient load scenarios in aerospace bearings subject to fluctuating axial loads. Precise calculations ensure the selected bearing load ratings align with operational demands, preventing overloading and extending service life.
Radial Load Calculation
Radial load calculation identifies forces perpendicular to the shaft axis. These forces often arise from the weight of components in horizontally positioned machinery.
Fr = Radial component of the external force
Radial loads are distributed unevenly across rolling elements and follow a bell-curve pattern. The force peaks directly under the load. In conveyor belts, load varies, and engineers simulate load points across the bearing using software. It optimizes radial load capacity without losing bearing integrity.
Axial Load Calculation
Axial or thrust load calculation focuses on loads parallel to the bearing’s axis. For accurate assessment, the force component along the bearing axis is isolated.
Fa = Axial (thrust) component of the external load
Axial bearing loads apply uniformly to rolling elements. Yet, off-center axial loads introduce moment forces. Additional factors, including load misalignment or angle, must be addressed in high-load hydraulic presses. Engineers also use trigonometry to resolve axial loads in multi-directional force systems. Hence, the bearing meets axial load capacity without structural compromise.
Combined Load Calculation
Combined load calculation assesses when bearings face both radial and axial loads. Engineers first calculate each load independently and then use formulas or load curves for combined effects.
P = XFr + Y Fa
Where,
In practical applications, engineers consult the technical manuals provided by manufacturers to determine the correct values of X and Y based on the specific bearing type and operating environment. In automotive wheel hubs, combined loads arise from radial weight and axial cornering forces, necessitating bearings that can withstand both types of loads. Accurate evaluation of combined loads is crucial, as miscalculations can lead to fatigue and premature bearing wear, particularly in dynamic load turbine shafts.
[The source of all the above calculations is PIB.]
Avoiding catastrophic breakdowns and maintaining mechanical systems requires accurate determination of bearing loads. Overloading occurs when the applied force exceeds the bearing’s dynamic or static load ratings, causing premature fatigue, distortion, and failure. Radial bearings with high axial loads may wear unevenly to trigger early failure and lengthy outages. On the other hand, underloading in preloaded angular contact bearings lowers frictional contact. It results in instability and excessive axial movement, which limits CNC spindle accuracy. The load type and bearing design must match when choosing bearings.
Deep groove ball bearings handle radial loads well. Yet, thrust or angular contact bearings manage strong axial forces better. Tapered roller bearings that bear axial and radial strains are ideal for vehicle wheel hubs. Bearings with smaller or ceramic rolling parts, including turbine assembly, mitigate centrifugal forces in high-speed applications. Load evaluation affects operating life and efficiency. Overloading a bearing diminishes its lifetime. However, well-matched bearing loads lengthen equipment life, decrease frictional losses, and optimize performance in high-stress conditions, including heavy-duty gearboxes and aircraft turbines.
We concentrate on precision-engineered angular contact, deep groove, and cross-roller bearings for high-precision applications under heavy loads. With heightened surface treatments and material selections, TPI improves operational stability in high-load automotive, machine tool, and electric motor applications. Our expertise includes decreasing rotational friction and wear while increasing thermal and load-bearing efficiency to accomplish industrial requirements with customized manufacturing for each sector.