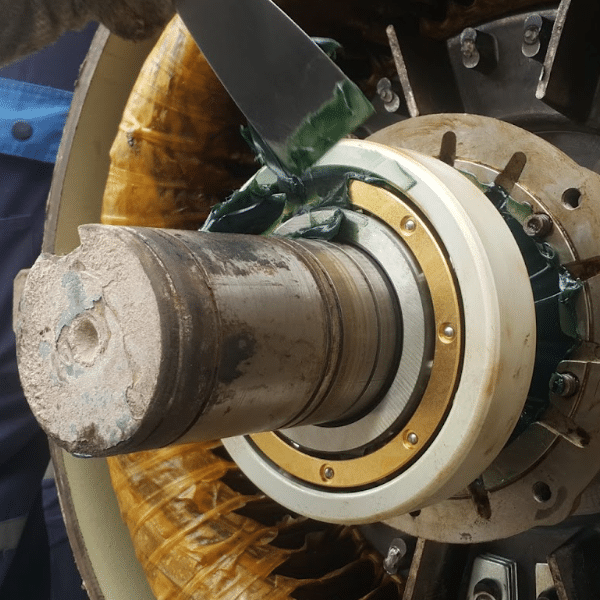
Learn how to identify, prevent, and address motor bearing failure with this in-depth guide. Discover common causes, warning signs, and proven maintenance strategies to avoid costly downtime.
Learn how to identify, prevent, and address motor bearing failure with this in-depth guide. Discover common causes, warning signs, and proven maintenance strategies to avoid costly downtime.
Motor bearing failure can be a significant setback for any industry relying on electric motors for its operations. The repercussions of such failures often result in downtime, increased maintenance costs, and, in severe cases, catastrophic equipment damage. This is why understanding the underlying causes of motor bearing failure is crucial for developing effective prevention strategies.
This guide takes a look at the common causes of motor bearing problems, like lack of lubrication and electrical erosion, and offers practical tips to reduce these risks. If you’re looking to maximize the lifespan and performance of your electric motors, then keep reading.
One of the primary advantages of sleeve bearings is their low maintenance requirements. Unlike ball bearings, sleeve bearings do not have moving parts such as balls or rollers, which reduces the need for regular lubrication and maintenance. Additionally, sleeve bearings are typically more cost-effective than ball bearings in terms of initial cost and long-term maintenance. Their simple construction and fewer components make them less expensive to produce, and their durability under low-stress conditions means they often last longer without requiring attention.
Sleeve bearings are best suited for applications where low to moderate speeds and light loads are involved. They are commonly used in fans, blowers, and electric motors, where their ability to operate quietly and efficiently under light loads is highly valued. In these environments, sleeve bearings provide a cost-effective solution that delivers adequate performance without high precision or frequent maintenance. For example, sleeve bearings are preferred in cooling fans due to their quiet operation and lower cost, making them an excellent choice for consumer electronics and home appliances.
Motor Bearings facilitate power transmission and maintain precise shaft alignment. These bearings are crucial components that support the rotation of the motor’s shaft. It is an essential piece for motors to run smoothly and efficiently. However, like any other mechanical component, motor bearings are subject to wear and tear and so, when it fails, it can lead to a costly downtime.
Here are some consequences of motor bearing failure:
Bearings support rotational movement and reduce friction between parts. Thus, when the bearing fails, it causes unscheduled downtime, improper motor function, or worse, a shutdown. Consequently, this disrupts production processes and daily operations and potentially leads to a loss in revenue.
When the motor bearing fails, it can lead to secondary damage to other components of the motor, such as the stator, rotor, and shaft. Without the bearings, the motor shaft will rub against the different parts of the motor, causing more friction and vibration. Eventually, it leads to further damage which means more extensive repairs or worse, a motor replacement.
An unexpected shutdown is the last thing anyone wants to happen. Hence, emergency repairs are typically more expensive due to the urgency of the situation. In addition, technicians and spare parts may not be readily available too, plus, things like expedited shipping for parts and unscheduled maintenance all the more make emergency repairs even more costly.
That being said, addressing motor bearing issues early on can not only optimize and improve efficiency but also significantly extend your motor’s life span, reduce energy consumption, and lower operational costs.
Abnormal sounds are often signs of bearings that are starting to fail. Audible sounds such as squealing, rumbling, or grinding noises are the earliest signs that components of a bearing are degrading. Metal particles or dirt in the grease can cause this too. As the failure progressively worsens, the noise also tends to intensify. Insufficient lubrication, improper bearing installation, or misalignment are some possible causes of the unusual noise.
As bearings wear down, vibration levels can rise. Minor flaws in the raceways and rolling elements may lead to impact forces during rotation, hence, producing these vibrations.
Regular monitoring can help detect these issues before they cause some serious damage or a complete motor failure.
Bearing temperature increases during operation. If not carefully kept track of, it may become overheated. Lubrication failure in the bearings is the most common reason for temperature rise and rapid deterioration. Excessive load leads to massive internal heat as well, which radiates to the bearings and accelerates lubricant deterioration. Apart from this, load imbalances can be particularly problematic if left unchecked. They create stress points within the bearing, leading to friction and overheating.
Addressing overheating early and monitoring motor temperature can prevent motor failure, improve overall efficiency, and extend the lifespan of the bearings.
Varnish vapour may get into the bearings if the varnish wasn’t dried enough. When this happens, the varnish vapor will react with bearing grease and lead to corrosion within bearings. As a result, these bearings will have reduced efficiency and a shortened lifespan.
Misalignment can sometimes occur during the installation process or because of a worn-out component. Uneven stress on the bearings is a result of a motor shaft that is not properly aligned with the load. This leads to premature wear and tear and accelerates motor failure.
High temperatures or high levels of moisture are considered extreme operating conditions for bearings. These conditions can degrade both the bearings and the lubricants. The humidity can lead to condensation inside the motor, therefore, causing corrosion. Meanwhile, high temperatures may break down the oil film, leading to metal-to-metal contact and accelerated wear.
Improper installation techniques, such as failing to align the bearing correctly or using incorrect tools can introduce excessive stress or deform the motor’s bearing. Misalignment and premature failure can also occur from over-tightening or under-tightening fasteners.
Electrical erosion occurs when stray electrical currents pass through the bearing instead of following a proper grounding path. This is also known as electrical pitting due to the pattern left in the bearing raceway. This can lead to surface degradation and eventually bearing failure. To prevent these issues, proper grounding techniques or the use of electrically insulated bearings are recommended.
To effectively reduce the likelihood of motor bearing failure, it is essential to conduct regular alignment checks, adhere to proper installation procedures, have ample consideration of environmental factors, and properly implement correct preventive maintenance practices.
Routine inspections should include checks for noise, temperature spikes, and vibrations to detect early signs of damage and wear in bearings. Regular maintenance reduces downtime, and for optimal safety, preemptively replacing or servicing bearings ensures that potential issues are avoided.
Bearing issues can arise from both under-lubrication and over-lubrication. It is recommended to follow manufacturer’s guidelines closely and monitor lubrication levels regularly. Properly determining the intervals and quantities for re-greasing is essential for optimal performance. Equally important is choosing the right type of lubricant as well as observing the timely application of lubrication.
Installing seals is the most effective method to significantly decrease the risk of bearing failure caused by contamination. Maintaining a clean environment helps prevent abrasion and corrosion by keeping contaminants like dirt, dust, and moisture at bay.
Bearing pitting and surface degradation can result from electrical discharge or arcing. By using electrically insulated bearings or installing groundings to properly discharge stray currents, damage to bearings can be avoided.
In conclusion, proper installation procedures and regular maintenance are crucial for ensuring the longevity and optimal performance of bearings. Additionally, paying attention to environmental factors such as contamination control and monitoring for electrical discharge can also prevent potential bearing failure.
By implementing these prevention strategies, businesses can avoid costly downtime and ensure that their equipment continues to operate efficiently. By staying proactive with bearing care, businesses can save time, money, and resources in the long run.
For a deeper understanding of how different bearing types can influence motor performance and efficiency, don’t miss the related article: Understanding Motor Bearing Types: Key Insights for Enhanced Electric Motor Efficiency.