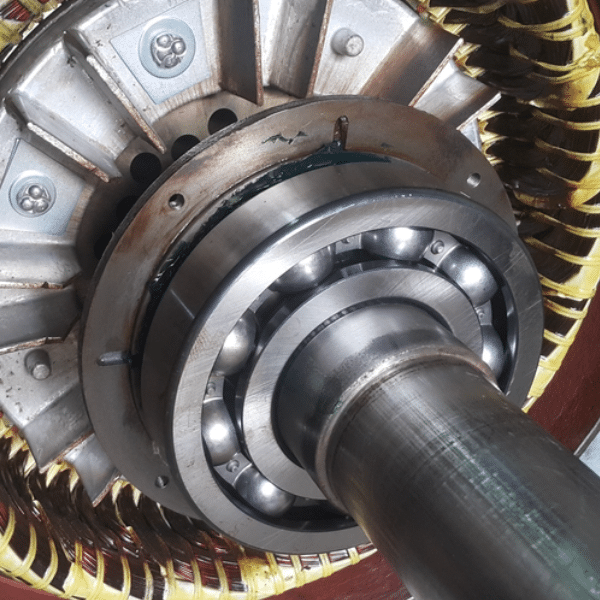
Discover the types, importance, and selection criteria for motor bearings with a guide on choosing the correct bearing for motor performance and life.
Discover the types, importance, and selection criteria for motor bearings with a guide on choosing the correct bearing for motor performance and life.
Electric motor bearings are precision-engineered to lower friction and provide regulated rotational motion within prescribed axes to transmit the load from the rotating shaft to the motor housing. They use rolling parts (balls and rollers) or journal surfaces in contact with the shaft to decrease wear under dynamic, heavy loads. Deep groove ball bearings provide quiet performance at high speeds. Meanwhile, angular contact bearings bear radial and axial stresses. Spherical roller bearings handle huge, misaligned loads in conveyors and crushers.
In variable-frequency motors, bearings with better insulation (ceramic hybrids) avoid electrical pitting and boost service life. Bearing selection, lubrication, and monitoring are key. For example, high-quality electric motor bearings rated at 100,000 hours may double motor life with less frictional heat, which can otherwise reach hazardous levels around 150°C. Consequently, motor bearings maintain mechanical stability, save expensive repairs, and preserve motor efficiency and durability in complicated, high-stakes industrial situations.
Ball motor bearings, deep grooves and angular contact types, are used in electric motors for their low friction and high-speed capacity. TPI’s precision grades (P4 and P2) are notable for CNC spindles and high speed motors, which need accuracy. TPI has enhanced the DmN value of high-speed motor-specific bearings to 1.5 million through optimized internal bearing design and lightweight, high-strength cages.
Roller bearings, available in cylindrical and spherical types, are designed to handle high radial loads and misalignment conditions, making them suitable for demanding industrial applications.
Cylindrical roller bearings excel in managing thermal expansion, making them ideal for heavy-duty equipment. Spherical roller bearings accommodate up to 2-3° misalignment, providing flexibility for applications requiring precision and durability. With proper material selection and precision assembly, roller bearings can endure shock loads and maintain reliable performance over extended working hours.
Sleeve (or plain) bearings offer durability in heavy-load, low-to-moderate speed applications. Unlike rolling bearings, which demand precise alignment, sleeve bearings better tolerate minor shaft misalignments and contaminants. They work without rolling elements and depend instead on a lubricated sleeve surface. Henceforth, it renders them resilient against frequent stop-start cycles in high-load environments. Compared to rolling element bearings, sleeve bearings have lower upkeep costs and a longer life. It might reach numerous years with lubrication in continuous-operation motors, including large HVAC and pump systems.
Axial loads act along the motor shaft’s axis. They need bearings that can endure forces pushing or pulling along this line. Despite their usage in radial load scenarios, deep groove ball bearings handle moderate axial loads due to the large contact area between balls and raceways. This design enables them to manage axial forces up to a significant proportion of their radial load capacity. Yet, cylindrical roller bearings shine in high axial load applications since the cylindrical rollers create a broad line contact with the raceways for better axial load-bearing capacity. For instance, single-row cylindrical roller bearings can handle substantial axial forces when those forces are unidirectional and consistent.
Radial loads, which act perpendicular to the motor shaft, demand motor bearings that can sustain force distribution around the entire shaft circumference. Angular contact ball bearings suit radial loads due to their contact angle, which distributes forces across a wide area for lower localized stress on each rolling element. Their load-bearing potential is maximum when the angle matches with the force’s direction. For instance, high-precision motors in CNC machines employ paired angular contact ball bearings. Each bearing is optimized at a contact angle of 15-40 degrees and is capable of supporting continuous radial loads that constitute a significant portion of their axial capacity. It also cuts frictional losses and heat generation for extended operational life.
Combined loads involve simultaneous radial and axial forces. They demand bearings that can accommodate multi-directional forces without losing stability. Spherical roller bearings are ideal for this purpose. Their dual rows of asymmetrical rollers provide a self-aligning feature that compensates for shaft deflections or housing misalignments. Spherical roller bearings are used in conveyor drives. These bearings can handle forces that represent a substantial portion of their total load capacity in combined load scenarios.E.g., large industrial motors equipped with spherical roller bearings can manage continuous radial and axial loads that closely approach their dynamic load rating, ensuring minimal deformation and resistance to stress during extended operational cycles.
Knowing load type is key to bearing selection. Apart from angular contact ball bearings, radial loads might also be handled by cylindrical or needle roller bearings for high load-carrying capacities due to their line contact across rollers. For heavy axial loads, cylindrical roller bearings are perfect, but angular contact or thrust ball bearings can also be used. They transfer loads along the shaft axis to prevent misalignment. Tapered or spherical roller motor bearings are suitable when a motor experiences combined radial and axial loads. They distribute the load across the inner and outer raceways. For instance, a tapered roller bearing in an industrial gearbox might be designed to bear 70% radial and 30% axial load.
High-speed applications demand bearings with low friction and heat generation. Deep groove ball bearings can be ideal here. However, angular contact ball bearings also work well at high speeds thanks to their optimized geometry for combined loads. At lower speeds, sleeve or journal bearings perform under heavy radial loads with lower maintenance needs, including handling below 1,000-3,600 RPM in industrial equipment. Hybrid ceramic bearings with ceramic rolling elements are also appropriate for extreme speeds. They offer better durability and lower lubrication needs.
Bearings must endure a range of environmental stresses. High-temperature conditions, including kiln motors, need motor bearings with polyurea-based grease that can tolerate up to 200°C. Sealed or shielded bearings in contamination-prone areas prevent dust, water, or particles from entering for a smooth operation. Anti-fretting is vital in vibration-heavy settings. Along these lines, in motorized conveyor systems, coated roller bearings resist fretting corrosion with a barrier against metal-on-metal wear. Hydrodynamic bearings are practical for systems exposed to water or aggressive contaminants for an additional shield.
High-voltage applications, like variable-speed motors, can result in stray currents causing electrical pitting. Insulated or ceramic hybrid bearings must be used for these cases. They block electrical paths within the bearing. For example, coated bearings resist up to 500 VDC for a barrier against electrical erosion. In wind turbines, ceramic hybrid bearings prevent pitting and dissipate heat under high loads. So, considered for all large motors above 100 kW, insulated motor bearings may extend bearing life while blocking harmful current paths.
Torque requirements affect bearing choice. For low-torque, high-precision applications, thin-section bearings maintain efficiency and decrease resistance. In noise-sensitive HVAC systems, deep groove ball bearings guarantee quiet operation at high speeds with lower dBA levels. Bearings with precision cage geometries, including angular contact bearings, cut vibration while stabilizing rolling elements. It is key to the accuracy of CNC spindles. With controlled noise and vibration, such bearings improve system accuracy and life.
At TPI, we offer precision-engineered Angular Contact Ball Bearings (designed for axial and radial loads), Deep Groove Ball Bearings (high rotational speed support), for bearing replacements or upgrades. TPI’s Hybrid Ceramic Bearings minimize friction and prolong durability for high-performance modifications in low-maintenance machines. Optimized internal designin TPI bearings improve load-bearing and heat resistance for electric motors and heavy machines. Contact us for inquiries or further assistance.