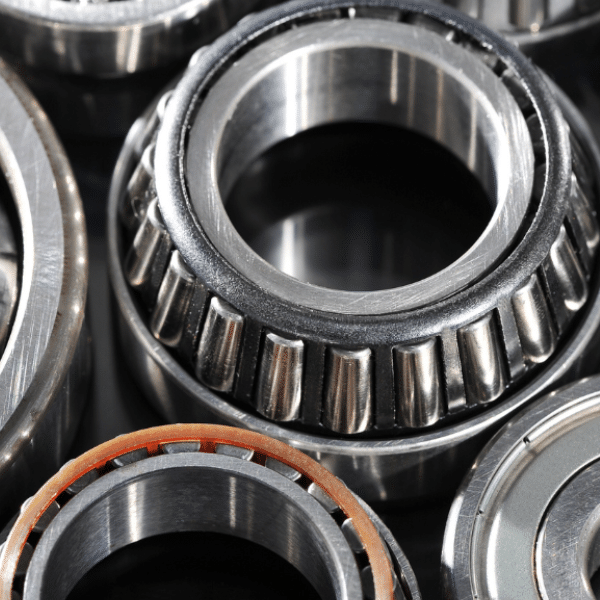
Learn the key differences between axial and radial loads and how they impact bearing performance. Discover expert tips for selecting the right bearing type for your machinery and application.
Learn the key differences between axial and radial loads and how they impact bearing performance. Discover expert tips for selecting the right bearing type for your machinery and application.
Bearing selection is a critical aspect of machine design and maintenance. This is why understanding the difference between axial and radial loads is crucial for making informed decisions about your motors, machinery, or mechanical systems. Choosing incorrectly can prematurely wear out even the best equipment, as bearings respond differently to each type of load. We will explore the distinctions between axial and radial loads and their impact on bearing performance, while providing guidance on how to select the appropriate bearing for your specific needs and application.
Bearing loads can be divided into two main categories: axial and radial.
Axial load is also known as thrust load and often occurs in applications where there is a need for controlled linear movement or where there is a need for supporting heavy weights. Axial loads are the forces that are oriented along the rotation axis of a shaft. The loads can be either a pulling or a pushing force along the shaft of the bearing. A bearing has to be perfectly aligned in order to prevent any movement or displacement along the axis; the force will be parallel to the axis and the shaft will be supported by a bearing.
This type of load includes forces generated by gears, or direct pushing and pulling actions. Examples include car transmissions, hydraulic cylinders, and even helicopter rotors.
Radial load is also known as normal or tangential load and often occurs in applications where there is a need for supporting weight that acts at 90 degrees to the shaft. This type of load exerts pressure perpendicular to bearing bore and outer diameter.
Examples of radial loads include the weight of a rotating wheel, centrifugal forces in turbines, and even human body weight on bike pedals.
Axial Load | Radial Load |
|
|
|
|
|
|
Thrust loads are forces that act parallel to the axis of rotation, either in an axial or radial direction. These forces can be static or dynamic and are typically caused by heavy external loads or pressure.
Thrust loads are a distinct category of axial loads, occurring when an axial force is applied in a single direction along the shaft of a bearing. Radial loads can also have a thrust component when the load incorporates an angular element, impacting both the radial and axial axes. Both axial and radial loads play an essential role in the performance of rotating machinery. Understanding these forces is crucial to selecting the right bearing for a particular application.
Axial and radial loads can really affect how well bearings perform and how long they last. If loads are too high or not applied correctly, they can cause bearings to wear out, get damaged, or even fail. So, it’s important to think about both axial and radial loads when choosing a bearing for a specific application to make sure it works perfectly.
The efficiency as well as the durability of the bearing is dependent on the load distribution inside it. For example, if a bearing is made for radial loads, then it should function smoothly under radial stress. If the bearing is designed for axial loads, then the load distribution must be in line with that. When a bearing is exposed to both types of loads, then the load distribution should be optimized to accommodate both and ensure maximum performance.
For instance, a bearing that is perfect for axial loads (like a thrust ball bearing) will appear weak for heavy radial ones. In this case, the axial and radial loads must be kept in check to ensure that neither of them exceeds the bearing’s capacity.
It is important to consider the loading types when designing the right car to ensure the bearings last as long as they should. Bearings designed to handle significant radial loads must endure repetitive stress and harsh service conditions without compromising their wear resistance. Similarly, bearings subjected to environmental factors, such as fluid pressure or solid particle intrusion, must possess sufficient durability to accommodate shaft displacement caused by misalignment or dynamic loads. Using the wrong bearings, like a radial ball bearing instead of one meant for axial loads, can slash their life expectancy by half.
Radial ball bearings are the most common type of bearings used to handle radial loads and consist of an inner and outer ring with balls between them to reduce friction. They have a higher load capacity than other types of bearings, making them suitable for applications with moderate to heavy radial loads such as car wheels and electric motors. They also have low torque levels, which means they require less power to operate.
On the other hand, roller bearings are designed to handle both axial and radial loads by distributing the load over a larger surface area compared to ball bearings. They can also tolerate misalignment better than ball bearings due to their self-aligning capabilities. Roller bearings come in various types such as cylindrical, spherical, and tapered.
Cylindrical roller bearings are designed to handle high radial loads and to moderate low axial loads. They have a higher load-carrying capacity than ball bearings due to their larger contact area, making them suitable for heavy-duty applications such as wind turbines and industrial machinery.
Spherical roller bearings are designed to handle heavy radial loads and moderate axial loads in both directions. They have a spherical outer ring raceway that allows misalignment and compensates for shaft deflection, making them suitable for applications with high shock or impact loads such as mining equipment and vibrating screens.
Tapered roller bearings, as the name suggests, have tapered rolling elements and are designed to handle both radial and axial loads. They can tolerate large amounts of thrust load in one direction while providing precise positioning in the opposite direction, making them ideal for applications such as vehicle wheel hubs and conveyor systems.
These are just a few examples of commonly used roller bearings. Other types include needle roller bearings, thrust roller bearings, and cam followers.
Selecting the right bearing requires a comprehensive evaluation of factors beyond load type to ensure optimal performance, cost efficiency, and longevity. Follow these key steps for effective selection:
Practical Tips for Selection
By following these streamlined steps, you can confidently select bearings that meet your application’s demands while ensuring reliability and efficiency. For more detailed insights, explore this helpful guide on bearings for radial and axial loads. Contact us to inquire about the most suitable bearing solutions for your needs.