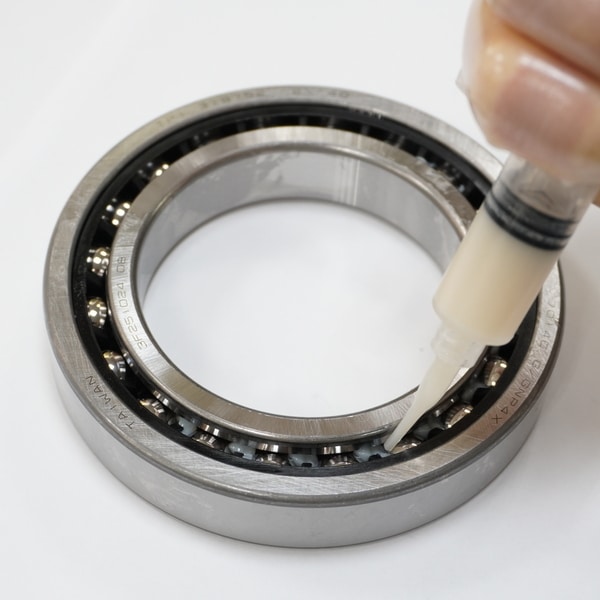
Learn about the most common causes of bearing failures, such as lubrication issues, installation errors, and overloading, and explore practical strategies to prevent these failures and extend bearing life.
Learn about the most common causes of bearing failures, such as lubrication issues, installation errors, and overloading, and explore practical strategies to prevent these failures and extend bearing life.
Bearings are critical components in a wide range of machinery, from small household appliances to large industrial machines. When bearings fail, they can cause significant damage to the equipment they support, leading to costly downtime, expensive repairs, and potential safety hazards. Bearing failures occur when the bearing can no longer perform its intended function, typically due to a combination of factors that cause excessive wear or damage to the bearing raceway.
Understanding the common causes of bearing failure is crucial for maintenance engineers and operators. Identifying potential issues early makes it possible to address them before they lead to catastrophic failures. This proactive approach not only helps extend the lifespan of bearings but also maintains the overall efficiency and reliability of machinery. For more on the basics of bearing failures, click here.
Lubrication is essential for the smooth operation of bearings. It reduces friction between rolling elements and the bearing raceway, minimizes wear, and helps dissipate heat generated by the bearing’s motion. However, lubrication problems are among the most common causes of bearing failure.
Improper installation is another major cause of bearing failures. Even the best quality bearings can fail if they are not installed correctly.
Material fatigue and wear are natural processes that occur as a bearing operates over time. However, certain factors can accelerate these processes, leading to early bearing failure.
The environment in which a bearing operates can significantly impact its lifespan. Severe conditions can accelerate wear and lead to premature failure.
Bearings are designed to handle specific load capacities. The bearing can experience accelerated wear or catastrophic failure when these limits are exceeded.
To prevent bearing failures and extend their service life, following best practices in lubrication, installation, and maintenance is essential.
Proactive maintenance and monitoring are key to preventing bearing failures. Regular inspections, along with the use of advanced monitoring tools, can help detect potential issues before they lead to significant damage.
TPI Bearings are known for their high quality and adherence to strict environmental standards. Their products are designed to meet the demanding requirements of various applications while offering cost-effective solutions without compromising on performance.
Understanding the common causes of bearing failure and taking proactive steps to prevent them can save your business from costly downtime and repairs. For more detailed information and to explore TPI’s range of high-quality bearings, visit the TPI Home Page. With TPI Bearings, you can trust that your machinery will operate smoothly and efficiently, backed by a company committed to quality and customer satisfaction.